工場での井水活用:法令遵守から高効率運用まで完全ガイド
工場での井水利用に関する法的要件、許可申請プロセス、高効率空調システムの設計、水質管理、予防保全型メンテナンス、TCO削減効果、環境負荷軽減、地域社会との共生について包括的に解説。持続可能な水資源管理の実践方法や先進的取り組みも紹介し、法令遵守から地域貢献まで、工場の水資源管理における重要ポイントを網羅的に説明しています。
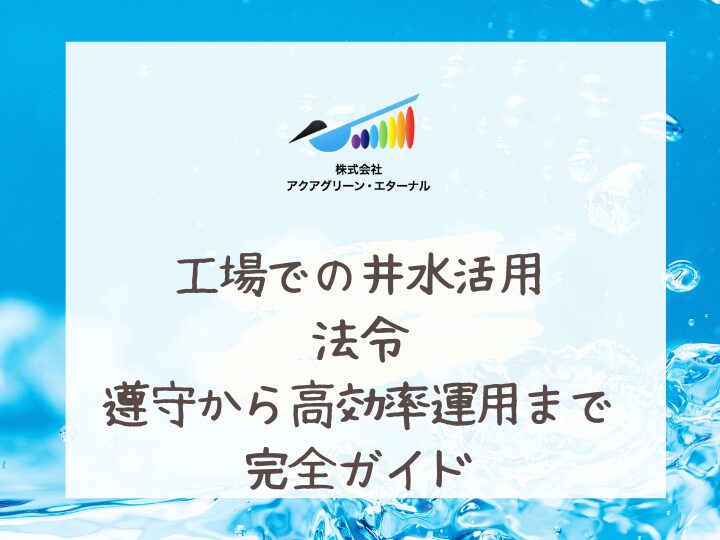
井水利用の法的要件と許可申請プロセス
工場での井水利用を検討する際、法令遵守は最重要事項です。地下水の汲み上げには、都道府県知事の許可が必要であり、その取得プロセスは複雑で時間を要します。許可申請には、取水量、用途、周辺環境への影響など、詳細なデータの提出が求められます。
特に注意すべき法律として、工業用水法、建築物用地下水の採取の規制に関する法律、水質汚濁防止法があります。これらの法律は地域によって適用が異なるため、事前に自治体との綿密な協議が不可欠です。
許可申請のプロセスは以下の通りです:
1. 事前相談:自治体の担当部署との詳細な打ち合わせ
2. 調査・計画:地質調査、水文学的調査、取水計画の策定
3. 環境影響評価:周辺地域への影響を科学的に分析
4. 申請書類作成:技術的根拠を含む詳細な書類の準備
5. 審査:自治体による厳密な審査(現地調査を含む)
6. 許可取得:条件付き許可証の発行
このプロセスには通常6ヶ月から1年程度かかるため、十分な準備期間を確保することが重要です。また、許可取得後も定期的な報告や監査が義務付けられることがあります。
井水を活用した高効率空調システムの設計と最適化
井水を利用した空調システムは、エネルギー効率と環境性能の両面で優れた選択肢です。特に、水冷式ヒートポンプと組み合わせることで、COP(成績係数)が4.0を超える高効率な冷暖房が可能となります。
システム設計においては、以下の技術的要素を考慮する必要があります:
1. 水質管理:
– TDS(全溶解固形分)、硬度、pH、微生物活性などの詳細な分析
– 逆浸透膜(RO)や電気脱イオン(EDI)などの高度浄化システムの導入
2. 熱交換効率の最適化:
– プレート式熱交換器やシェル&チューブ式熱交換器の適切な選択
– フーリング係数を考慮した余裕のある伝熱面積設計
3. ポンプシステムの効率化:
– インバータ制御による可変流量システムの採用
– キャビテーション防止のための適切なNPSH設計
4. 排水処理と再利用:
– 冷却塔ブローダウン水の処理と再利用システムの構築
– 中水利用による水資源の有効活用
さらに、井水の温度変動を考慮したシミュレーション解析を行い、年間を通じた最適運転パターンを策定することが重要です。これにより、従来のエアコンシステムと比較して、30-50%のエネルギー削減が可能となります。
高度な水質管理と予防保全型設備メンテナンス
工業プロセスにおける井水の利用では、水質管理が重要課題です。具体的には、以下のパラメータを定期的にモニタリングする必要があります:
– pH:6.5-8.5の範囲内に保つ
– 硬度:100mg/L以下(CaCO3換算)
– 濁度:5NTU以下
– 全鉄:0.3mg/L以下
– 遊離塩素:0.1-0.3mg/L
これらの管理には、オンライン水質分析計と連動したフィードバック制御システムの導入が効果的です。例えば、pHの変動に応じて自動で中和剤を注入するシステムなどが挙げられます。
設備メンテナンスについては、予防保全の観点から以下のアプローチを推奨します:
1. 予知保全:
– 振動解析によるポンプ劣化の早期検知
– 赤外線サーモグラフィによる熱交換器の性能低下診断
2. 定期点検:
– 超音波流量計による配管システムの漏水チェック
– 内視鏡カメラによる配管内部のスケール堆積状況確認
3. 化学洗浄:
– EDTA系キレート剤を用いた定期的なスケール除去
– 生物膜除去のための適切な殺菌剤の選定と投与
これらの高度な水質管理と予防保全策により、システムの安定稼働と長寿命化が実現し、ライフサイクルコストの大幅な削減が可能となります。
井水利用によるTCO削減と環境負荷軽減の定量的評価
井水利用システムの導入によるTotal Cost of Ownership (TCO)削減効果は、以下の要素を考慮して算出されます:
1. 初期投資:
– 井戸掘削費用:500-1,000万円(深度100-200m)
– 水処理設備:3,00-5,00万円
– 空調システム改修:1,000-2、000千万円
2. 運用コスト削減:
– 水道料金:年間200-1,000万円の削減(使用量に依存)
– 電力料金:年間500-2,000万円の削減(COP向上による)
3. メンテナンスコスト:
– 年間50-200万円(定期点検、消耗品交換等)
これらを考慮すると、典型的な中規模工場(延床面積10,000㎡程度)では、10年間のTCOで2-4億円の削減が見込めます。
環境負荷軽減効果については、以下の指標で評価できます:
– CO2排出量:年間500-1,000トンの削減(電力使用量減少による)
– 水資源保全:年間3-10万㎥の水道水使用量削減
これらの数値は、環境報告書やCSRレポートにおいて、具体的な環境貢献指標として活用できます。
地域社会との共生と持続可能な水資源管理の実践
工場での井水利用は、地域の水資源に直接影響を与える可能性があるため、地域社会との協調的な関係構築が不可欠です。具体的には以下のアプローチを推奨します:
1. 情報公開と対話:
– 定期的な住民説明会の開催(年2回以上)
– Webサイトでのリアルタイム取水量データの公開
2. 共同モニタリング:
– 地域の水文学者や環境NGOと協力した地下水位観測ネットワークの構築
– 観測データの共有プラットフォーム開発
3. 緊急時対応:
– 渇水時の取水制限ルールの策定と公表
– 地下水汚染発生時の即時通報システムの整備
4. 地域貢献:
– 工場見学会での水資源教育プログラムの実施
– 地域の水源涵養活動への参加(植林活動等)
さらに、持続可能な水資源管理の観点から、以下の先進的取り組みを検討すべきです:
– クローズドループ水処理システムの導入:工場内での水の100%再利用を目指す
– 雨水利用システムの構築:屋根面積を活用した大規模雨水貯留施設の設置
– AIを活用した最適取水管理:地下水位予測モデルに基づく動的取水制御
これらの取り組みにより、工場は単なる水の消費者ではなく、地域の水資源管理の中核的存在として機能することが可能となります。
以上の戦略的アプローチにより、法令遵守、高効率システム運用、環境負荷軽減、そして地域との共生を同時に実現する、先進的な工場水資源管理が可能となります。