Revolutionizing factory air conditioning: Water-cooled vs. air-cooled, a thorough comparison of efficiency, cost, and environmental friendliness
This book compares and explains the basic mechanisms, energy efficiency, operating costs, adaptability to installation environments, environmental impact, and maintainability of water-cooled and air-cooled air conditioners. Water-cooled types are highly efficient and economical in the long term, but require a water source and initial investment. Air-cooled types are easy to install but are less efficient. It is important to understand the characteristics of both types and make the appropriate choice based on the usage environment and operating conditions.
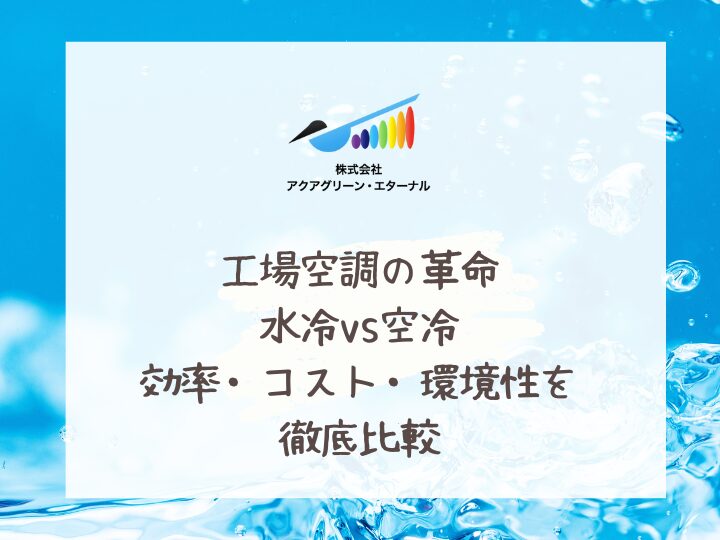
Basic mechanism of water-cooling and air-cooling
When selecting an air conditioning system for a factory, the main options are water-cooled and air-cooled air conditioners. Although the basic thermodynamic principles of both are the same, there is a big difference in the way heat is released.
Water-cooled air conditioners are based on the second law of thermodynamics and utilize the high specific heat capacity and thermal conductivity of water. The heat absorbed in the refrigerant cycle is efficiently transferred to water, which is then cooled in a cooling tower or groundwater system. This process effectively increases entropy while minimizing enthalpy change.
Air-cooled air conditioners, on the other hand, use the thermal capacity of the air to release heat. They use finned-tube heat exchangers to maximize surface area and promote heat transfer by forced convection. However, because air has a lower thermal capacity than water, a greater temperature difference and volume of air is required to release the same amount of heat.
Both systems use a refrigeration cycle based on the Carnot cycle, but the difference in how heat is ultimately released has a significant impact on the efficiency and range of application of the overall system.
Energy Efficiency and Operating Costs
In terms of energy efficiency, water-cooled air conditioners have an advantage over air-cooled ones. This is due to the fact that the heat transfer coefficient of water is about 25 times higher than that of air. As a result, the surface area of the heat exchanger required to achieve the same cooling capacity is significantly reduced, leading to a more compact and efficient overall system.
To give a concrete figure, under normal conditions, the COP (coefficient of performance) of a water-cooled system is about 5.0 to 6.0, while that of an air-cooled system is about 3.0 to 4.0. This difference has a significant impact on annual operating costs. For example, assuming a system with a cooling capacity of 1000kW is operated for 3000 hours per year, the water-cooled system can reduce power consumption by about 20 to 301 TP3T compared to the air-cooled system.
However, the initial investment cost is higher for water-cooled systems. This is because they require additional facilities such as piping, cooling towers, and water treatment equipment. Therefore, it is important to perform a comprehensive economic evaluation that takes into account the payback period. Typically, when the annual operating time exceeds 3,000 hours, water-cooled systems tend to be more economical in the long term.
Installation environment and adaptability
In terms of adaptability to the installation environment, both systems have distinct characteristics. Water-cooled air conditioners require abundant water sources, but have the advantage of being less susceptible to outside air conditions. This is because they use a thermodynamically stable heat source (water). They are particularly effective in areas with high outside temperatures, high-rise buildings, underground facilities, and other environments where contact with outside air is limited.
On the other hand, air-cooled systems have a high degree of freedom in installation and can be used in places where it is difficult to secure a water source. However, they are directly affected by the outside temperature, so their performance is easily affected by environmental conditions. For example, in environments where the outside temperature exceeds 35°C, the COP of air-cooled systems drops rapidly and may fall to around the design value of 70%.
Noise levels are also a factor to consider. With air-cooled units, the fan noise from the outdoor unit can be a problem, with noise levels typically around 65-75 dB(A). With water-cooled units, the main noise source is indoors, so proper soundproofing can enable quieter operation.
Environmental impact and sustainability
From the perspective of environmental impact, both systems have their own advantages and disadvantages. Water-cooled air conditioners are highly energy efficient and can reduce CO2 emissions during operation. Under typical operating conditions, water-cooled systems can reduce CO2 emissions by 15 to 251 TP3T compared to air-cooled systems.
However, care must be taken when it comes to water resource usage. In a typical water cooling system, about 2-3 liters of water evaporates per kWh. To minimize this water consumption, it is effective to introduce closed-loop cooling towers and grey water/rainwater utilization systems. With the latest technology, it may be possible to reduce water consumption to less than the conventional 50%.
Air-cooled systems are advantageous in areas with water shortages because they do not directly use water resources. However, they consume a lot of energy, which can lead to high indirect environmental impacts depending on the power source configuration. To address this issue, the adoption of high-efficiency inverter technology and combination with renewable energy sources such as solar power generation are effective solutions.
Maintenance and durability
Maintainability and durability are important factors that directly affect long-term operating costs and equipment reliability. Water quality management is extremely important for water-cooled air conditioners. If proper water treatment is not performed, scale formation and corrosion can reduce heat exchange efficiency, and in the worst case, lead to system failure. However, if properly managed, the lifespan of major components can last more than 20 years.
Routine maintenance includes:
1. Water quality analysis and adjustment (once a month)
2. Cleaning and inspection of cooling towers (twice a year)
3. Check the efficiency of the heat exchanger and clean it (once a year)
4. Refrigerant leak inspection (once a year)
Air-cooled systems do not require water quality control, so routine maintenance is relatively easy. The main tasks are as follows:
1. Clean the air filter (once a month)
2. Cleaning the outdoor unit fins (twice a year)
3. Refrigerant leak inspection (once a year)
4. Check the compressor oil (once a year)
However, air-cooled systems are exposed to the elements, so there is a high risk of corrosion, especially in coastal and industrial areas. To prevent this, applying corrosion-resistant coatings and regular rust prevention treatments are effective.
For both systems, preventive maintenance can be achieved by regularly conducting non-destructive testing using vibration analysis and thermography to detect potential problems early and minimize downtime.
In factories, the reliability of the air conditioning system is directly linked to productivity, so it is important to establish a planned maintenance system and secure a backup system. In addition, the introduction of a real-time monitoring system that utilizes IoT sensors enables early detection of abnormalities and efficient operation.