Revolutionizing factories! Well water heat pumps increase heating efficiency by 40% and dramatically reduce costs
Well water heat pumps are innovative systems that utilize the stable temperature of groundwater to significantly improve the heating efficiency of factories. They have a higher COP than conventional air heat sources and can reduce energy consumption by 30 to 401 TP3T. They offer multiple benefits, including the superiority of water cooling, sustainable water resource management, economic efficiency over the long term, and optimization of energy management throughout the factory.
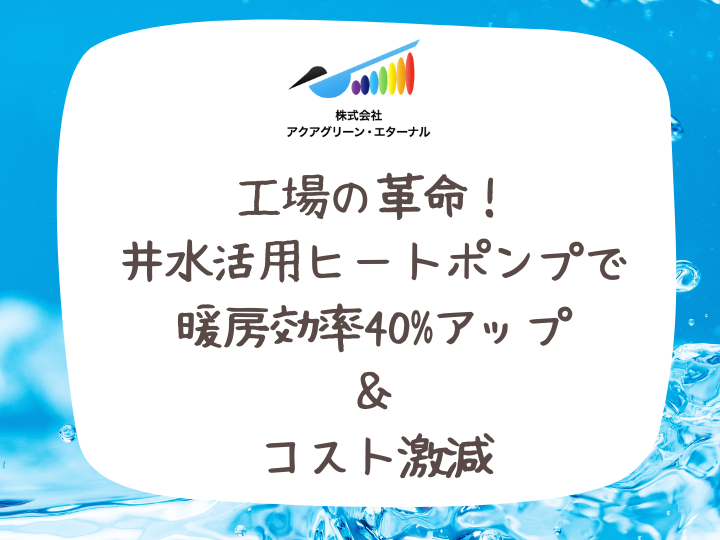
A highly efficient heating system that utilizes the stable temperature of well water
The use of well water heat pumps is an extremely effective means of improving heating efficiency in factories. By taking advantage of the yearly stability of groundwater temperature (10-15°C), an efficient heat source that is not affected by the outside temperature can be secured. From a thermodynamic point of view, this stable heat source maximizes the efficiency of the Carnot cycle and achieves the theoretically highest COP (coefficient of performance). Specifically, under the condition of an outside temperature of 0°C, the COP of a conventional air source heat pump is about 2.5-3.0, while a well water type can achieve a COP of 4.0-5.0 or more. This means that energy consumption can be reduced by 30-401 TP3T, which directly translates into cost savings of tens of millions of yen per year in large factories.
Advantages and thermodynamic considerations of water-cooled systems
The water-cooled system of a well water heat pump has excellent thermodynamic properties. The specific heat capacity of water (4.2 kJ/kg・K) is about four times that of air (1.0 kJ/kg・K), and it can transport about 3,300 times more heat in the same volume. This dramatically improves heat exchange efficiency and enables a compact design. In addition, the thermal conductivity of water (0.6 W/m・K) is about 25 times that of air (0.024 W/m・K), maximizing the performance of the heat exchanger. These properties simultaneously realize a compact and highly efficient system, contributing to the effective use of factory space. In addition, the low noise of the water-cooled system (usually less than 60 dB) also contributes to improving the working environment and labor productivity.
Achieving sustainable water resource management and reducing environmental impact
The well water heat pump is an advanced system that realizes sustainable water resource management. By returning the water after heat exchange underground, it maintains the groundwater level and conserves water resources at the same time. This circulation system is consistent with the groundwater flow model based on Darcy's law, and ensures the long-term stability of the groundwater environment. In addition, water circulation within the factory can reduce water consumption by up to 801 TP3T compared to conventional systems. This technology directly contributes to SDGs Goal 6 "Clean Water and Sanitation" and Goal 12 "Responsible Consumption and Production". In addition, it has a significant effect on reducing greenhouse gas emissions, which is an important step towards achieving carbon neutrality.
Design and life cycle cost analysis with a view to long-term operation
Appropriate design and maintenance planning are essential for the long-term operation of well water heat pumps. Water quality management is particularly important, and regular water quality analysis (pH, hardness, iron, etc.) and the introduction of an appropriate water treatment system based on the results are necessary. For example, the installation of anti-scale devices and iron removal filters can minimize the efficiency decline of the heat exchanger. A life cycle cost analysis including these measures shows that although the initial investment is 20 to 301 TP3T higher than that of conventional systems, the reduction in operating costs and the extended life of 15 to 20 years make it possible to reduce total costs by 30 to 401 TP3T. In addition, further energy savings can be expected by adopting inverter control, which is highly efficient during partial load operation.
Optimizing energy management throughout the factory
The introduction of a well water heat pump leads to the optimization of the energy management system (EMS) of the entire factory. For example, by mixing 60-70°C warm wastewater generated from the production process with well water (15°C) to create a heat source of 30-35°C, it is possible to improve the heat pump's COP to 6.0 or more. This integrated approach can improve the energy efficiency of the entire factory by 20-301 TP3T. Furthermore, by introducing predictive control using IoT and AI technology, it is possible to create an optimal operation plan linked to the production schedule and respond to peak cutting and demand response. This can also contribute to reducing electricity costs and stabilizing the power system.
From the above analysis, it is clear that well water heat pumps are not only an effective way to improve factory heating efficiency, but also an innovative solution that can achieve comprehensive energy saving, environmental protection and cost reduction. We strongly encourage factory managers and personnel to actively consider the introduction of this advanced technology, taking into account the characteristics of their own companies. Long-term investments will greatly contribute to strengthening the competitiveness and sustainable development of factories.