Revolutionizing factory air conditioning: Amazing energy savings achieved with water-cooling systems
The combination of refrigerant and water cooling in factory air conditioning systems is an innovative way to significantly improve energy efficiency. By utilizing the phase change of the refrigerant and the heat capacity of water, as well as the temperature stability of groundwater, significant energy savings can be achieved. Appropriate refrigerant selection, water quality management, and smart management using IoT and AI enable sustainable, highly efficient operation.
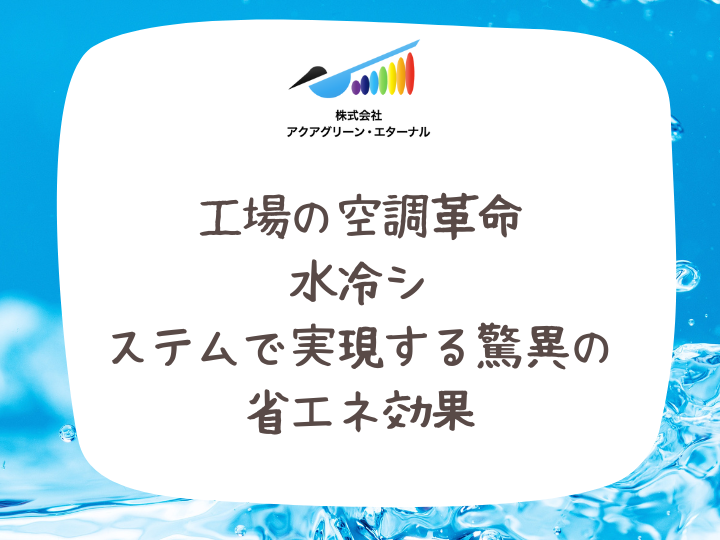
Refrigerant-water synergy: the key to increased efficiency
In factory air conditioning systems, the combination of air conditioner refrigerants and water cooling systems is an innovative approach that dramatically improves energy efficiency. The core of this method is the integration of the use of latent heat due to the phase change of the refrigerant and sensible heat transport by utilizing the high heat capacity of water.
Specifically, the refrigerant absorbs and releases a large amount of heat through its evaporation and condensation cycle, and the water efficiently transports that heat. In this process, by minimizing the difference between the refrigerant's phase change temperature and the water temperature, it is possible to reduce exergy loss and improve the COP (coefficient of performance) of the entire system.
For example, in a water-cooled chiller, heat exchange occurs between the refrigerant and water in the condenser. In this case, by using water cooled in a cooling tower, a stable condensation temperature can be maintained regardless of the outside air temperature. As a result, the workload of the compressor is reduced and system efficiency is improved. Furthermore, by combining it with a free cooling system, it is possible to stop the chiller during the intermediate and winter months and perform cooling only with water from the cooling tower, achieving significant energy savings.
Energy saving effect by using groundwater
Utilizing groundwater has the potential to dramatically improve the efficiency of factory air conditioning systems. The temperature stability of groundwater is a thermodynamically extremely advantageous property. It is based on the law of ground temperature, which states that the temperature generally rises by about 1°C for every 10m underground and remains almost constant throughout the year.
By taking advantage of this stable temperature characteristic, the efficiency of the heat pump system can be maximized. For example, by directly using 15°C groundwater in summer, the target temperature can be reached with much less energy than cooling 35°C outdoor air. Specifically, the electricity required to achieve the same cooling capacity can be reduced by more than 501 TP3T.
Furthermore, by introducing a water-to-water heat pump system that uses groundwater as a heat source, it can also be used efficiently for heating in the winter. In this case, even when the outside temperature is below 0°C, a high COP can be maintained by extracting heat from groundwater at around 15°C. Highly efficient operation with a COP of around 4 to 5 is possible throughout the year, and there have been reported cases where energy savings of over 601 TP3T have been achieved compared to conventional systems.
Key points for introducing a water cooling system
To effectively introduce a water cooling system, careful planning that takes the entire system into account is essential. First, the selection and evaluation of the water source is extremely important. When using groundwater, it is essential to secure the long-term water volume through pumping tests and to evaluate the risk of corrosiveness and scale formation through water quality analysis.
In system design, we consider cascade use, which makes the most of the temperature difference between the primary side (water source) and the secondary side (air conditioning load). For example, by using water in the process that requires the lowest temperature first, and then dissipating heat in a cooling tower, we can improve the thermal efficiency of the entire system.
Additionally, to respond to load fluctuations, we are considering adopting inverter-controlled pumps and fans and installing heat storage tanks, which will help level out peak power demand and contribute to reducing contracted power.
Furthermore, when integrating with existing systems, optimizing hybrid operation is key. For example, building a detailed control strategy is effective, such as prioritizing operation of the water-cooled system during partial loads and using the existing air-cooled system only during peak loads.
The importance of choosing the right refrigerant
The choice of refrigerant has a decisive impact on both system efficiency and environmental impact. Currently, the phase-down of F-gas is underway from an environmental perspective, and the adoption of next-generation refrigerants is urgently needed.
Next-generation refrigerants such as R32 and R290 have excellent thermodynamic properties, enabling systems to be more compact and more efficient. For example, compared to R410A, R32 requires approximately 301 TP3T less charge to achieve the same cooling capacity, and its theoretical COP (coefficient of performance) is improved by approximately 51 TP3T.
When combining with a water cooling system, it is necessary to pay attention to the relationship between the critical point of the refrigerant and the water temperature. A CO2 refrigerant (R744) system using a supercritical cycle can produce high-temperature water, which is particularly effective in factories with a demand for hot water. For example, it can produce hot water of 60°C or more at the same time as cooling, significantly improving overall energy efficiency.
In addition, when selecting a refrigerant, it is necessary to consider future regulatory trends and market changes with a view to long-term operation of the system. The adoption of natural refrigerants with low environmental impact (such as ammonia and CO2) is also worth considering as a sustainable option.
Tips for maintenance and operation management
To maintain a highly efficient water cooling system, systematic maintenance and operation management based on a scientific approach are essential. Particular attention should be paid to maintaining heat exchange efficiency and water quality management.
A decrease in the efficiency of the heat exchanger can cause an energy loss of 5% or more even with just 0.1mm of scale adhesion. To prevent this, we recommend regular chemical cleaning and constant online monitoring of the heat transfer coefficient. In addition, the use of a plate type heat exchanger makes it possible to both simplify disassembly and cleaning and improve efficiency.
In water quality management, it is important to balance corrosion and scale formation. Indicators such as pH, hardness, alkalinity, and conductivity are regularly measured and controlled within the optimal range. In particular, it is important to manage the Langelier Saturation Index (LSI) to prevent calcium scale formation. By maintaining the LSI within the range of 0 to 0.5, it is possible to properly form an anticorrosive film on piping while suppressing scale formation.
In terms of operation, it is effective to introduce a smart management system that utilizes IoT and AI. A sensor network is used to grasp the overall status of the system in real time, and machine learning algorithms are used to constantly calculate optimal operating parameters. This enables dynamic control in response to changes in outside air conditions and production status, realizing operation at the highest efficiency throughout the year.
In addition, visualization and detailed analysis of energy flows can continually identify opportunities for system-wide optimization. For example, pinch analysis can be used to explore the possibility of heat recovery and improve the thermal efficiency of the entire plant, which can serve as a long-term energy-saving strategy.
This comprehensive approach will maximize the benefits of installing a water cooling system and ensure sustainable factory operations.