Learn from the pros! How to improve the efficiency of water-cooled factory air conditioners and preventive maintenance
Cooling water quality management and regular inspections are essential for the efficient operation of water-cooled air conditioners. Failure to properly manage water quality can cause problems such as scale formation and corrosion, leading to reduced system efficiency and failure. Proper management of indicators such as pH, hardness, and electrical conductivity, and implementing water treatment programs according to the situation, will help maintain system efficiency and prevent downtime.
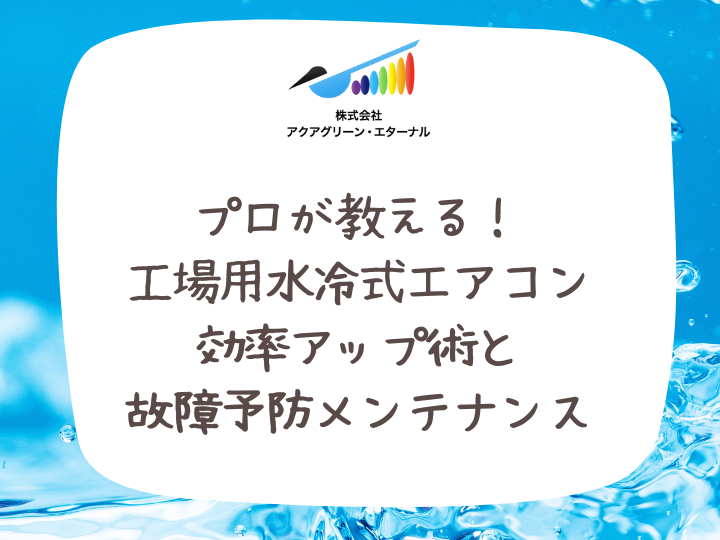
Cooling water quality management and regular water quality testing
Managing the quality of cooling water is an extremely important factor for the efficient operation of water-cooled air conditioners. In factory environments, groundwater or well water is generally used as cooling water, but these water sources are easily affected by seasonal and environmental changes, and are characterized by large fluctuations in water quality.
Failure to properly manage water quality can result in multiple problems, such as scale formation, corrosion, and microbial growth, which can lead to reduced system efficiency and failure. Indicators that require particular attention include pH value (preferably 5.8 to 8.6), total hardness (150 ppm or less), and electrical conductivity (400 μS/cm or less). If these values deviate from the allowable range, this can lead to reduced heat exchange efficiency and a shortened pipe life.
In addition, it is also important to manage the residual chlorine concentration (0.2 to 0.5 ppm) to prevent the proliferation of pathogenic microorganisms such as Legionella. Professional engineers will comprehensively analyze these indicators and select the appropriate water treatment agent and adjust the dosage. For example, they will create an optimal water treatment program according to the situation, such as using a scale inhibitor if the hardness is high, a neutralizer if the pH is low, and an appropriate disinfectant if microbial growth is a concern.
Regular water quality testing and proper water treatment will not only keep your system efficient, but will also help prevent unexpected downtime, making this an important investment that will directly translate into sustained productivity and long-term cost savings.
Heat exchanger cleaning and inspection
The heat exchanger is the core of a water-cooled air conditioner, and its performance determines the efficiency of the entire system. In a factory environment, fouling caused by impurities and microorganisms in the cooling water progresses at an accelerated rate, causing a decrease in heat exchange efficiency.
Heat exchanger maintenance by a professional technician goes beyond simple cleaning. First, non-destructive testing techniques (e.g. eddy current testing) are used to measure the thickness of the heat exchanger tubes and detect minute cracks. This allows potential failure risks to be identified in advance, allowing for planned repairs or replacements.
In the cleaning process, we select the most suitable cleaning agent and method according to the nature of the dirt (scale, slime, corrosion products, etc.). For example, we use an acidic cleaning agent for calcium carbonate scale and an alkaline cleaning agent for organic dirt, and we implement effective cleaning using a scientific approach. In addition, we prevent deterioration of the metal surface due to cleaning by neutralization and passivation treatment after cleaning.
This specialized maintenance allows the heat exchanger's heat transfer coefficient to be maintained at or above the design value of 95%, improving the overall system Coefficient of Performance (COP), which in turn reduces energy consumption and lowers operating costs.
Refrigerant system leak inspection and filling
The refrigerant system of a water-cooled air conditioner is a complex system that is repeatedly exposed to high and low pressure. Refrigerant leakage not only reduces the performance of the system, but also has the risk of impacting the environment and violating regulations. In particular, measures to prevent leakage are extremely important for legacy systems that use refrigerants with high ozone depletion potential (ODP) and global warming potential (GWP).
Our professional engineers use the latest leak detection technology to detect even the smallest leaks. For example, we use electronic leak detectors (sensitivity: 3g/year or less) and helium leak detectors (sensitivity: 10-9 Pa・m3/s) to perform highly accurate leak inspections. Non-contact leak inspections using infrared cameras are also effective and are used for efficient inspections, especially in large systems.
When a leak is confirmed, it is important not to simply replenish the refrigerant, but to analyze the root cause and take measures. For example, there are many causes of leaks, such as fatigue failure of the pipes due to vibration, tiny holes due to corrosion, and deterioration of the sealing material. We properly diagnose these causes and consider redesigning the pipes or changing the materials if necessary.
When it comes to refrigerant charging, it is crucial to manage the exact amount of charge based on the system's design specifications. Overcharging or undercharging can lead to reduced system efficiency and damage to equipment. Professional technicians are familiar with the physical properties of refrigerants (such as the relationship between pressure, temperature, and density) and can provide optimal charging while taking into account the operating conditions of the system.
Furthermore, the formulation of a transition plan to low GWP refrigerants will be an important issue for the future. Expert support will be essential for formulating facility renewal plans with an eye toward switching to next-generation refrigerants with lower environmental impact, such as R32 and HFO refrigerants.
Checking and adjusting the electrical system
The electrical systems of water-cooled air conditioners, especially those for large factories, are highly complex. They are an accumulation of advanced electronic technologies, including inverter control, automatic control by microprocessors, and the coordination of various sensors and actuators. Malfunctions in such complex systems can not only cause the air conditioning function to stop, but can also lead to the shutdown of the production line or a serious accident.
A professional electrical inspection will include advanced diagnostics and adjustments such as:
1. Thermal imaging diagnosis: Infrared thermography is used to detect abnormal heating of switchboards and connections without contact, allowing for early detection of poor contacts and overload conditions.
2. Harmonic analysis: A power quality analyzer is used to measure and analyze the harmonics generated by the system. Harmonics can cause equipment to malfunction or overheat, so measures such as installing filters can be taken if necessary.
3. Inverter diagnosis: Analyzes output waveforms and evaluates the characteristics of internal elements (IGBT, etc.) to determine the deterioration state of the inverter. This allows for planned part replacement and renewal.
4. Optimization of sequence control: We analyze PLC (Programmable Logic Controller) programs to improve control logic and optimize operation for energy conservation.
5. Sensor Calibration: Check the accuracy of measuring instruments such as temperature sensors and pressure sensors, and calibrate them if necessary. Highly accurate sensor signals are essential for stable system operation and energy-saving control.
These professional inspections and adjustments can improve system reliability, improve operational efficiency, and reduce the risk of unexpected outages. In addition, the use of the latest technology to manage electrical systems, such as the introduction of predictive maintenance systems using IoT and AI technology, will also become an important trend in the future.
Compressor performance evaluation and preventive maintenance
The compressor, the heart of a water-cooled air conditioner, is a critical component that determines the efficiency and reliability of the entire system. In large factory systems in particular, a sudden compressor failure can have a significant impact on production activities. Therefore, it is extremely important to always keep the compressor in optimal condition and perform planned maintenance.
Compressor performance assessment and preventive maintenance by professional technicians involves the application of advanced techniques such as:
1. Vibration analysis: An acceleration sensor is used to analyze the vibration spectrum of the compressor. An increase in vibration in a specific frequency band suggests a specific failure mode, such as bearing wear or rotor imbalance. Fast Fourier Transform (FFT) analysis allows for early detection of even minute abnormalities.
2. Oil analysis: Compressor oil components are analyzed periodically to evaluate the presence of metal particles and the degree of oxidation. This allows for a non-destructive diagnosis of the wear condition of internal parts and the deterioration of the oil.
3. Current signature analysis: The compressor motor current waveform is sampled with high precision,
This technique detects electrical faults such as broken rotor bars and shorted stator windings.
It is possible to detect electrical abnormalities at an early stage.
4. Thermal efficiency analysis: Collect data such as compressor intake and discharge temperatures, power consumption, etc.
, calculate the isentropic efficiency. Track the change in this value over time.
This allows you to understand the performance deterioration trend of the compressor.
5. Ultrasonic diagnosis: Uses high-frequency ultrasound to detect abnormal noises and friction sounds inside the compressor.
This method makes it possible to detect early abnormalities that are too small for the human ear to hear.
.
Infrared Thermography: Using an infrared camera, the surface temperature of the compressor is measured.
Visualize the temperature distribution. Localized overheating may indicate increased internal friction or poor cooling.
there is.
The combination of these advanced diagnostic techniques allows for a comprehensive assessment of the compressor's condition.
For example, vibration analysis can be used to determine the optimum maintenance plan for bearings.
If initial wear of the parts is detected, it will be evaluated together with the oil analysis results and replaced at the appropriate time.
Plan for product exchange.
Furthermore, by accumulating and analyzing this data over the long term, predictions can be made using machine learning and AI.
This advanced approach will also enable the creation of a comprehensive maintenance system.
By minimizing the risk of sudden breakdowns of the equipment, and maximizing the operating rate and life cycle through planned maintenance,
This allows for a reduction in shipping costs.
Professional maintenance by professional technicians is not just a matter of troubleshooting, but also a way to improve your water-cooled air conditioner.
The aim is to optimize the entire system and maintain long-term performance. Regular diagnosis and appropriate prevention
Conservation leads to improved energy efficiency, reduced operating costs, and increased overall plant productivity
It will make a big contribution.
Factory managers and personnel must understand the importance of these specialized maintenance methods.
We recommend that you make appropriate investments and implement them in a planned manner.
I want to convey that long-term facility management will ultimately bring about significant economic benefits.
I think so.