The secret of water-cooled air conditioners: How highly efficient cooling works and optimal maintenance methods
Water-cooled air conditioners are highly efficient air conditioning systems that utilize the excellent thermal conductivity of water. The main components are a refrigerator, cooling tower, circulation pump, piping system, and indoor unit. They are characterized by high heat exchange efficiency, energy saving, stable performance, and long life. Water quality management, pipe inspection and cleaning, filter management, and cooling tower maintenance are important to maintain the efficiency of the system.
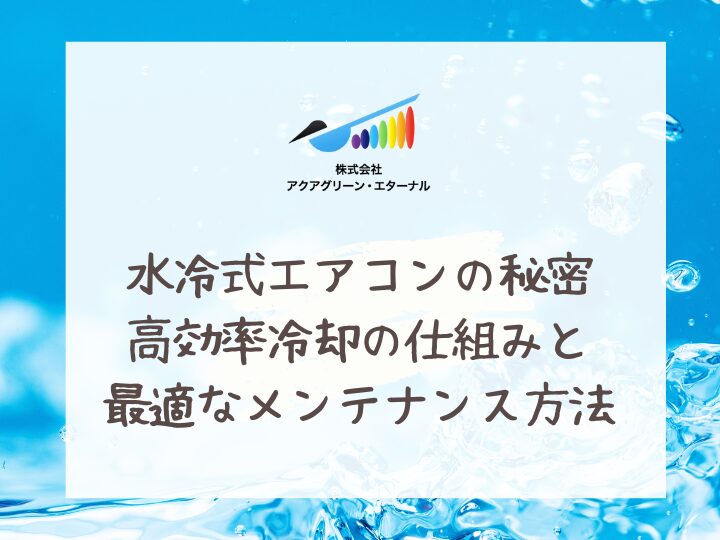
Understand the basic mechanism of water-cooled air conditioners
Water-cooled air conditioners are highly efficient air conditioning systems that are widely used in factories and large commercial facilities. At their core is a heat exchange process that utilizes the excellent thermal conductivity of water. Specifically, water (or antifreeze) cooled by a refrigerator is circulated through a piping system and the air is cooled by passing it through the coils of the indoor unit. This method has the following advantages over air-cooled systems:
1. High heat exchange efficiency: The specific heat capacity of water is about four times that of air, allowing for more efficient heat transfer.
2. Energy saving: High heat exchange efficiency means less energy is needed to achieve the same cooling capacity.
3. Stable performance: It is less affected by outside temperature and can maintain stable cooling capacity throughout the year.
4. Long service life: Since the main equipment is installed indoors, it is less susceptible to deterioration due to wind, rain, or direct sunlight.
The main components of the system are the chiller, cooling tower, circulation pump, piping system, and indoor unit (fan coil unit and air handling unit). Efficient air conditioning is achieved by properly coordinating these elements.
Checking and Managing Water Quality: Key to System Efficiency
In water-cooled air conditioners, water quality control is essential to maintain performance. Inappropriate water quality can cause various problems, such as reduced heat exchange efficiency, corrosion of pipes, and scale formation. Therefore, it is important to regularly monitor the following parameters and keep them within the appropriate ranges:
1. pH value: ideally in the range 7.0-8.5. Below this there is an increased risk of corrosion, above this there is an increased risk of scale formation.
2. Electrical conductivity: Generally, it is desirable to keep it below 800µS/cm. If it is too high, there will be a lot of dissolved solids, and the risk of corrosion and scale formation will increase.
3. Total hardness: Ideally 50-150ppm CaCO3. Too high a hardness will lead to scale formation.
4. Chloride ion concentration: 200ppm or less is desirable. High concentrations of chloride ions accelerate the corrosion of metals.
5. Total alkalinity: 100-300ppm CaCO3 is appropriate. This is related to pH stability.
To properly manage these parameters, it is effective to take the following measures:
1. Introduction of automatic water quality analyzers: Monitors water quality in real time and detects abnormalities early.
2. Use appropriate water treatment agents: Add appropriate amounts of corrosion inhibitors, scale inhibitors, biological control agents, etc.
3. Blowdown Control: Dissolved solids concentration is controlled by periodically draining a portion of the circulating water and replacing it with fresh water.
4. Regular professional water analysis: This will allow for more detailed analysis and identify long-term trends.
Inspecting and cleaning piping systems: maintaining efficient heat transfer
The piping system is an important element of a water-cooled air conditioner, and can be considered the "blood vessels." To maintain efficient heat transfer, it is essential to carry out regular inspection and cleaning, paying attention to the following points:
1. Leak check: Use ultrasonic flow meters and infrared cameras to detect even the smallest leaks.
2. Check the condition of the insulation: Deterioration of the insulation increases heat loss, so it should be inspected regularly and replaced if necessary.
3. Evaluating the cleanliness of the inside of the pipe: An endoscopic camera is used to visually check the condition inside the pipe.
4. Chemical cleaning: If scale or sediment buildup is found, chemical cleaning should be performed using an appropriate cleaning agent. It is important to select a cleaning agent that is compatible with the pipe material.
5. Mechanical cleaning: Physical cleaning using brushes and scrapers is also effective, especially on the heat exchanger area.
6. Hydrodynamic Cleaning: High pressure water is used to flush and physically remove deposits.
By carrying out these cleaning operations in a planned manner, the heat transfer efficiency of the system can be maintained for a long period of time. It is also important to measure the heat exchange efficiency before and after cleaning operations to quantitatively evaluate the effect.
Cleaning filters and strainers: protecting your system
Filters and strainers play a vital role in protecting your system by removing impurities from the circulating water. A strategic approach to managing these devices can be effective:
1. Differential pressure monitoring: The pressure difference before and after a filter or strainer is constantly monitored to determine the degree of blockage.
2. Introduction of an automatic backwash system: By introducing a system that automatically performs backwashing when a certain differential pressure is reached, the frequency of maintenance can be reduced.
3. Multi-stage filtration: By using a series of filters, from coarse to fine, the lifespan of each filter can be extended.
4. Material selection: Select a filter material with excellent corrosion resistance and durability depending on the usage environment.
5. Regular visual inspection: Conduct regular visual inspections to detect any physical damage or deterioration of the filter element at an early stage.
It is also recommended to measure the filtration efficiency before and after cleaning using a particle counter to quantitatively evaluate the performance of the filter after cleaning.
Cooling Tower Inspection and Cleaning: Optimizing Heat Rejection Efficiency
Cooling towers play a vital role in water-cooled air conditioning systems by transferring heat back into the atmosphere. To keep them performing optimally, a comprehensive approach is required:
1. Efficiency evaluation of filler: Quantitatively measure heat transfer efficiency to understand the deterioration of filler performance. In general, if the efficiency falls below the design value of 85%, replacement is considered.
2. Preventing scale buildup: Add appropriate water treatment agents to the cooling water to prevent scale formation, and clean the filler regularly to maintain heat transfer efficiency.
3. Microbial control: Use appropriate disinfectants to prevent biofilm formation, especially Legionella, by periodically adding effective disinfectants such as sodium hypochlorite and chlorine dioxide.
4. Drift Control: Highly efficient drift eliminator is used to minimize water loss and impact on the surrounding environment.
5. Maintaining fan efficiency: Regularly clean and adjust fan blades to keep airflow at an optimum level, and use inverter controls to ensure optimal operation according to load.
6. Water quality monitoring: Automatic water quality analyzers are installed to constantly monitor pH, conductivity, ORP (oxidation-reduction potential), etc. This allows us to respond to changes in water quality in real time.
By implementing these measures comprehensively, it is possible to maintain optimal cooling tower performance over the long term and contribute to improving the efficiency of the entire system. It is also important to conduct periodic thermal performance tests to quantitatively evaluate the actual performance of the cooling tower.